Choosing the Correct Synthetic Sling for Your Lift
Written by Dave Decker, President, Becket Training & Consulting in Crane and Rigging Hotline
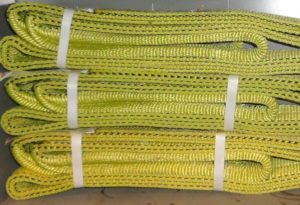
Synthetic slings can be a great choice for many lifting applications. Whether you choose synthetic rope slings, webbing slings, or roundslings, they are relatively light weight compared to steel slings with similar capacity. Synthetic slings are easy to transport and can often be rigged by a single person, making them a great choice for general purpose lifting.
Synthetic slings can be made from a variety of materials, but most commonly, they are made from either nylon or polyester. These two materials are very similar in appearance and may be difficult for anyone but the most experienced person to distinguish by sight alone. This is one reason you must always consult the sling identification before using any sling to make a lift.
But does it really matter what type material they are made from? Well, yes it does. First of all, it matters when choosing a sling for its ability to absorb shock or to control stretch under load. Nylon slings are very elastic. They may stretch up to 10 percent under full load, depending on the construction of the sling. They tend to resist transfer of shock loads to the crane better than most other sling materials. Polyester slings, on the other hand, may stretch only half as much, and consequently will transfer a bit more momentary load to the crane if a shock load occurs. Other synthetic sling materials including high performance fiber slings will have different characteristics.
When a sling is used in a chemically active environment, it is imperative to choose a sling that will not be adversely affected. Chemical agents may be found in the air or on any surface that the sling may contact. Nylon slings are known to be easily damaged by contact with acids for example. Lifting a pallet of lead acid batteries with nylon slings would be ill advised. Polyester slings on the other hand, would likely be damaged if exposed to caustic agents, such as lye, found in an industrial cleaning tank. Every sling material may be susceptible to damage by different chemical agents. The sling manufacturer or qualified person should always be consulted before any slings are used in chemically active environments.
When working with hot materials or in extremely hot or cold environments, nylon or polyester slings may not be the best choice. These slings should not be used at temperatures in excess of 194°F (90°C) or below −40°F (−40°C).
We would be remiss if we failed to consider sling abrasion. Abrasion can adversely affect any sling. A sling made from synthetic materials can suffer abrasive damage or even melting at room temperature due to friction caused by movement over a surface while loaded. Always consider the effects of abrasion and the various ways you can protect the sling during use. For example, you can purchase slings made with sewn on wear pads, or you can apply pads at the point of contact. You should always try to minimize sling movement over any surface during a lift. Abrasion protection alone may not be adequate to protect slings from cutting. Protection from cutting should be considered any time a sling is used over an edge.
So how can you be sure you are using the right sling for the job? Every sling has a tag or other identifying markings that list, at a minimum, the synthetic sling materials and rated load(s) as well manufacturer’s name, trademark or logo. If any part of the tag is missing or illegible, the sling is not suitable for use and should be removed from service.
It is up to you to make sure that you choose the best sling for the job. Further, you must use it in accordance with OSHA regulations, ASME B30.9, and the manufacturer’s instructions. Always consult the manufacturer or a qualified person whenever there is a question as to the suitability of a particular sling for a particular application.
Article provided by Dave Decker, President, Becket Training & Consulting,www.cranetrainingexpert.com